|
Post by sdb777 on Mar 14, 2010 7:20:30 GMT -6
It's been a long search, but I think I've settled on a speaker design! Although none of the drivers I have in boxes will work, I can probably trade a few to get the drivers I'll need(they seem to be discontinued and in high demand? who'd thunk that??) Kind of 'borrowed this photo' from another forum.....my bad, didn't see any copyright info imbedded on/in it.  I know! Not a simple design at all....but hey, think of the new stuff I'll need to buy to make them!?!?!? Don't tell the wife! Here's one question: How would you go about reverse engineering this design? I know the driver(speaker) to be a FE108Sigma (link to speaker specs: www.fostexinternational.com/docs/speaker_comp/pdf/fe108sigma.pdf ) or I could just tell you it is a 4" full range driver. And at the base of the speaker, I'm thinking that those are cement patio blocks that are 8"x8"x1-1/2"....maybe? The original builder of this speaker has not returned a few PM's/emails in the last week(not sure what to think of that?). So I can't get schematics or build plans.... From what I can obtain about the speaker through the topic on it: #1) There are two main 'pieces' in the design. The round 'ball' housing the driver, and the 'horn' for the back pressure. a) The 'ball' housing the driver is actually a very good design! It will not reflect any unwanted frequencies towards this listening area....this design is found on some very 'high end' speaker cabinets costing in excess of $3K b) The 'horn' is made from a 'jig'(except for the outside pieces). Not sure what the equipment was to cut it? But I'm thinking a router....maybe? Here's another question: What kind of tools are going to be required?-I have a jigsaw, although it is a piece of crap. -I have some clamps that will open to 18"(think I have 6 of them) -I have a nice lathe....not sure about turning MDF(to make the 'ball'?) -I have a skillsaw, mitersaw, tablesaw with some nice blades....but I think those are not going to be needed? And yet another question: How many sheets of 3/4" MDF will be needed?Guesses are just fine. I'm sure more questions will arise as I get closer to actually doing this project, but for now these questions are all I can think of! Scott (better assemble them in place...sure look heavy) B
|
|
|
Post by Leo Voisine on Mar 14, 2010 7:31:58 GMT -6
Wow - you don't go after the easy ones do you?
I would make a template in a piece of cardboard (poster board) from a local craft store.
Trace is out onto some 1/8 or 1/4 MDF.
Cut it out with you jig saw.
Fair out all the curves so there are NO bumps or divits.
The thin MDF will be a template.
Not using your MDF template - trace out the pattern onto the thick Ply or MDF for the speaker carcase.
With the jig saw cut is out 1/4 over sized - it does not need to be pretty.
Now with a pattern bit in a Porter Cable Router series 690 ;D ;D you can clean up the thick MDF.
Cut out as many pattern as you need.
CAREFULLY glue together no more than two at a time. Cause you will not be able to keep more than two lined up.
After the sheets are glued up - sand the edges till the cows come home.
Use a corner rounding bit to radius all around the preiphery.
|
|
|
Post by deepsplinter on Mar 14, 2010 7:48:10 GMT -6
If I was building this thing? I'd go about it exactly like Leo said.
With one exception. I'd go get a Ridgid Oscillating Belt/Spindle Sander. ;D
|
|
|
Post by sdb777 on Mar 14, 2010 9:38:43 GMT -6
Thanks Leo!
I know it's probably not the easiest design, but then I don't really plan on building more then one set(unless I could find a local market for them, and the money was right! And it looks as though it would need to be a boat-load of money!!!).
This would be for my personal use only.
I like the idea concerning the template and using my crappy jigsaw! This would also increase the (KTWH factor)-Keep The Wife Happy factor!!! And the glueing of two pieces at a time is wonderful advise....could see me now swearing at the wood for moving around.
Any idea how to make a schematic from this photo? Scale for build, or whatever it would be called??
BTW, I'll be building my own amplifier for this project also. A Dyna 'clone' ST70 tube amp(35w per channel) and trying to find a vintage Dyna PAS3 tube pre-amp(plenty of gain). The Dyna ST70 kit was ordered this morning(don't tell the wife it costs a little)! Still looking for the pre-amp? Found a few, but I'll hold out for a better deal. You might be thinking, just use your Adcom equipment.....that's the same thing the wife said. But I want pure sound....already got mind-numbing. And with all of the available power from the Adcom, I'd be blowing drivers faster then I could replace them.
Scott (keep those ideas coming) B
|
|
|
Post by sdb777 on Mar 14, 2010 9:46:11 GMT -6
If I was building this thing? I'd go about it exactly like Leo said.
With one exception. I'd go get a Ridgid Oscillating Belt/Spindle Sander. ;D Thanks. Not that I'm questioning your advise about being able to purchase a new 'toy'..... But wouldn't there be a higher chance of 'over sanding' with a spindle sander? I'm not going to get many pieces to work with out of a sheet of MDF(and the cost of the stuff isn't going down). I did a search on the Ridgid model you mentioned, it's not that bad on the wallet....but I'm still worried about the 'damage' I could do. Scott (new 'toys' are alway cool though) B
|
|
|
Post by deepsplinter on Mar 14, 2010 10:00:13 GMT -6
I was 'bout half kidding about the sander. Unless it turns out you're gonna be making quite a few speakers like that.
Like any machine, you can do damage with it, but with a little experience on one, I'm thinking it would be a time saver.
If you're just gonna make two of 'em, some sandpaper wrapped around your finger or a dowel rod would get ya by.
|
|
|
Post by Leo Voisine on Mar 14, 2010 11:12:48 GMT -6
I thought about the OSS - but I don't think it would be big enough.
Reason I said about the template was not so you could many of them - I know your gonna do just two. The template allows you to make the many pieces you will need.
If you even watched David Marks make an exotic design - he always makes a template.
After the template is made - and you use a router to make the patterns you will be able to make matching shapes. When you glue them up you will have minimal sanding to do.
If you simply trace on MDF then cut with a jig saw - you will never be able to make exact copies on many pieces.
To make a scale drawing of what you see in the picture will take a little skill - but not really too bad. Think about using coffee cans, or other round objects to trace. Then real thin strips of wood to bend into the longer arcs. Once you trace onto poster board you can cut it out with scissors. After looking at it - you might modify it - till you achieve what you are looking for.
Sure there are a lot of steps - but how else would you do it?
I have watched David Marks do it over and over many times.
|
|
Joe Lyddon
WoW Member
Banned.
Sam Maloof & I Dec. 2, 2005
Posts: 2,507
|
Post by Joe Lyddon on Mar 14, 2010 11:39:24 GMT -6
Yes, I would make the template & cut the parts as Leo says... BUT... How do you know what is possibly on the INSIDE of it? Is there audio being channeled from the top speaker (ball) to the lower section & vise-versa? Where would you put the baffles, etc.? Is each section (top, & bottom) in and of itself without any audio connection to the other? How is the audio being handled internally? Am I being too suspicious? ;D Looks like a unique enclosure all right! Would sure be a conversation piece! ;D ;D 
|
|
|
Post by TDHofstetter on Mar 14, 2010 15:15:28 GMT -6
I think the most interesting parts will be the inside & outside curved flat faces. The sides (the "saxophone profile") will probably take about one sheet per two speakers unless I've got the scale all wrong - they look like about 5' tall. If they're only 4' tall, you'll easily get four sides from one sheet. Maybe six.
Yep, them bendy curves will be interesting... because you can't kerf-bend them unless you backfill with Bondo or something. They need to be full thickness all the way through each of the curves or they'll color your sound.
|
|
Joe Lyddon
WoW Member
Banned.
Sam Maloof & I Dec. 2, 2005
Posts: 2,507
|
Post by Joe Lyddon on Mar 14, 2010 16:19:43 GMT -6
Some layers of that flexible bendable 1/8" plywood? Glued to ribs screwed around the edge... with the ply on the inside of the outside sides so the edges wouldn't have to be covered?
|
|
|
Post by TDHofstetter on Mar 14, 2010 16:50:11 GMT -6
I'm thinkin' the horn would want to be form-bent and form-laminated FIRST, then wiggle strips added, the flat sides applied to it & trimmed to shape.
|
|
|
Post by sdb777 on Mar 14, 2010 18:06:36 GMT -6
Yes, I would make the template & cut the parts as Leo says... BUT... How do you know what is possibly on the INSIDE of it? There is nothing on the inside of the horn....Is there audio being channeled from the top speaker (ball) to the lower section & vise-versa? Yes, the sound coming from the back of the driver follows the curves and generates the low wave....Where would you put the baffles, etc.? There are no baffles on the interior.....Is each section (top, & bottom) in and of itself without any audio connection to the other? There is only the one full range driver. No crossover needed from the ampilifier.....How is the audio being handled internally? The lower octaves are generated by the lenght of the horn, with no other help....Am I being too suspicious? ;D Nope, all very valid questions....Looks like a unique enclosure all right! Would sure be a conversation piece! ;D ;D That is some of the reason behind the unique design, but not the whole reason. Horns are beautiful to listen to.Thanks for the interest. I'll definitely need to do a complete write-up with photo's on this journey! Scott (too much fun) B
|
|
|
Post by sdb777 on Mar 14, 2010 18:26:00 GMT -6
I think the most interesting parts will be the inside & outside curved flat faces. The sides (the "saxophone profile") will probably take about one sheet per two speakers unless I've got the scale all wrong - they look like about 5' tall. If they're only 4' tall, you'll easily get four sides from one sheet. Maybe six. Yep, them bendy curves will be interesting... because you can't kerf-bend them unless you backfill with Bondo or something. They need to be full thickness all the way through each of the curves or they'll color your sound. I may be wrong, but I believe the two outside pieces are part of a 'sandwich'? Sort of like taking a pile of MDF and cutting the internal pieces, then glueing them together....no bending necessary. If you look at the photo, you'll see the layers of MDF(towards the top inside curve)....I'll crop and circle the area for a better look. 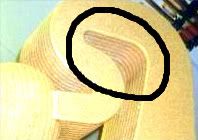 Hope this works..... I count a total of 12pieces(2sides and 10cutouts). That's my width 12x1/2=6" wide! And yes, 4' would be great to reduce waste! At 5' it would generate so much waste I'd probably get into some serious trouble when the wife sees what's going on! And I don't think I could get away with telling her, "It's better then buying the finished product, shipping, and then someone to help me move them in the house!" Scott ('coz I don't think I'd be in the house anymore) B
|
|
|
Post by sdb777 on Mar 14, 2010 18:44:33 GMT -6
Or 12 pcs @ .75" = 9.0".......
Scott (don't know the scale) B
|
|
|
Post by Leo Voisine on Mar 14, 2010 19:50:41 GMT -6
Scott - YES - sandwiched together.
That is EXACTLY - what I am talking about.
Many patterns - sandwiched together.
|
|
Stretch
WoW Member
Mark Muhr
Posts: 461
|
Post by Stretch on Mar 14, 2010 19:57:16 GMT -6
Yeah, any way you go about it, you're going to have a lot of waste. Some of the waste will get used to make the balls, but you're still going to have quite a bit of waste making those cutouts to make it hollow. If you end up making them 5' tall, you can get 10' long mdf, but I wouldn't want to be the one moving them. Just brainstorming here, but have you considered making them out of fiberglass? You make the sides out of MDF, throw in some temporary spacers, then stretch the fiberglass fabric over the curves. Build up a few layers of cloth and resin and you're done. I don't know if the acoustical quality will be what you're after, but I have seen high end car speaker boxes done this way.
|
|
|
Post by TDHofstetter on Mar 14, 2010 20:35:50 GMT -6
HOLY GODS! If those are all cut outta' STACKED SHEETS... that's a VAST amount of waste.
Tell ya what. Work up the curvy parts from stacked laminations. The flat straightaways between curves can be MDF boardstock. That'll save a TON of waste. You could then use scraps to make up the stacked curves - a stack for the front & a stack for the back. If ya make 'em carefully & lay 'em up with the straightaways in place, it'll save a bunch of fitting after the stacks are glued.
|
|
wisardd1
WoW Member
Account Removed by own Request.
Posts: 261
|
Post by wisardd1 on Mar 14, 2010 22:51:45 GMT -6
One question: Why?
|
|
|
Post by sdb777 on Mar 15, 2010 5:41:50 GMT -6
Ah.....why. Well, I guess it comes down to making something that will have superior music quality over what I could buy in a store somewhere. And knowing I made it right. It's sort of like seeing folks use a dovetail joint on a box.... When glue and a nail would do just as good(but that just wouldn't be right, at least not for me) Or building a box when you could buy one at a store for 1/10th of the price(but that just wouldn't be right, at least not for me either). Love answering why..... Another example. Why don't we all drive Fords? After all, Henry Ford had a great design, and no one should have bothered to build something else if the original was good enough.....right? But someone, somewhere thought that they could do something better....and then they made it themself, differently. Scott (why not) B
|
|
|
Post by Leo Voisine on Mar 15, 2010 10:40:50 GMT -6
If ya make a pattern our of posterboard 50 cents - you can lay that on a sheet of ply and optimize the sheet usage.
My CAM software will do that too. If I have time I just might be able to make a design and maybe mount a pen in my CNC mackine and draw a pattern on a piece of poster board.
Once I had a pattern I can optimize in onto a sheet of MDF and know exactly how to cut it out and exactly how much would be needed.
I could than send the pattern to you. I would cut the pattern into 8x11 pieces to make it easier to ship.
It would be interesting to do.
My size constraints would be 24"x24" --- though, I could to it in sections if you want it bigger.
If you are interested - let me know.
|
|