|
Post by RiverWalker on May 3, 2010 22:02:27 GMT -6
So after some of the information you all helped with in my other thread, I'm working on figuring up a design for a workbench, and looking through the workbench book.
a few things come to mind that I am looking for opinions on.
at the moment, the space available to me is carpeted. no way around that, and nothing to be done about it. how much of a problem is that, really? and which style of bench-foot(I mean, the sled kind where the leg mortises into a horizontal piece, or just the leg going straight to the floor directly) might be better for being on carpet, and/or which do you prefer in general and why.
I am figuring for the legs to be two 2x4's each. would getting actual 4x4's instead, be substantially better?
I am figuring probably for the top to be around 2' deep and 4' long, this is shorter than the ones I seem to be seeing, now is this just because bigger is usually better, and leaves more options for larger projects, or does having it that size make it less stable?
Height. now I'm sure this one is highly debated and a matter of opinion, but I'm curious what people do for their own, and what their personal reasoning is for their choice. I'm 6'2", and I have absolutely no idea what sort of direction I should go on this.
and lastly, for now, what method of fastening mortices for a workbench, would you recommend? there seems to be a huge variety of methods to hold it together, and I'm not clear on exactly what is the least-better-best scale on which is which, or if most of them are about the same functionally, and its largely a matter of style and ability to take it apart, or what.
|
|
|
Post by TDHofstetter on May 3, 2010 22:10:57 GMT -6
Just for perspective... for years of my adult life, I worked wood on a workbench 4' long, with 2-2x4 legs. I didn't have any great problem with it. Now that I've got 8'-long workbenches, I find that they fill up just like the 4' one did, only when they're full there's a lot more stuff to put away.  On a carpeted floor, it's kindest to the carpet to put full skids under the legs to spread the bench's load as much as you can. A bench may at times be loaded with a lot more weight than ordinary furniture. You may find that the bench will bounce a little on the carpet, especially if it's got a pad under it, and so any sort of hammering operation may be a little unusual-feeling. Possibly a little more tiring than usual, too. For height... I like my benchtops to be just about tall enough for me to place my hands flat on, with my arms straight down, elbows bent just a tiny bit. Too low & you'll lean over to work, too high & your arms'll get tired fast. The joinery... as you say, there are nearly countless choices. That part... I'll leave up to you. 
|
|
|
Post by dicklaxt on May 4, 2010 5:37:53 GMT -6
Why can't you remove the carpet,if you leave it you are going to have to remove it in the near future anyway,,,,,,,,,,,,,wear patterns,spills,abrasives working on carpet fibers etc
dick
|
|
|
Post by dcarter636 on May 4, 2010 9:06:35 GMT -6
The popular height for a hand tool bench is somewhere between the tops of the front pockets of your Levi's (hoisted up to where the belt wraps around your waist), and the belt of said Levi's. I use the tops of my pockets because it is comfortable for hand planing as well as chisel work. The appropriate size of the leg stock depends on how they are braced, and attached to the top; bigger is better but using well fastened 2x6 or 2x8 stretchers between those legs will add substantial rigidity to the support structure. I don't consider anything less than 4x4 for legs and use at least 2x6 for stretchers near the bottom and near the top of the legs. This oak bench support structure is for a 32"x72" hand tool bench it is rock solid due to the dual stretchers and glued mortise and tenon joinery.  This construction lumber support structure is fine for power tools and light hand tool work but it would go wobbly in a very short time with heavy hand planing work. Note 36"x48" maple top on 4x4 DF legs and 2x6 hemlock stretchers screwed to the legs. 
|
|
sawduster
Moderator
The Motley Crew
Posts: 1,831
|
Post by sawduster on May 4, 2010 9:54:24 GMT -6
Another consideration for leg design is the type of front vise you intend to install. For instance, if you intend on installing a leg vise (in my opinion, the most economical and useful front vise), you will want to design such that the front of the front legs are flush to the front edge of the bench top. You might also want, in the case of a leg vise, designing such that the top front stretcher is flush to the front of the legs and the bench top, and possibly beefing up the width of that stretcher so you can drill dog/hold fast hole into the stretcher. This allows additional versatility to the front vise allowing you to better secure wide pieces as shown in the pic below.   The above pic shows another view of the previous set-up. Note the piece of scrap of the same thickness as the work piece inserted on the opposite side of the vise screw to prevent the vise from racking.
|
|
|
Post by Safetyboy on May 4, 2010 10:28:17 GMT -6
Lot's of good feedback already, but I'll give my $0.02: Feet - straight leg feet are fine if your legs are big enough. Sled feet are obviously more time-consuming to build. Legs - laminated legs are fine. My bench legs are 5"x3", glued up from 4 pieces of 1x stock. Top - bigger adds weight to the bench, which helps stability. And there's NEVER enough bench top space for all your parts / tools / scraps, etc. Height - One recomendation is where you little finger joins your hand, should meet the bench top when your arm is loose at your side... that feels a little low to me, so my bench is a bit higher. Might take some adjusting, so build it a little tall - it's easy to cut some off the legs. Joinery - M&T is generally the best you can do (wedged or drawbored even better), but not simple to take apart. For something simpler, My 1/2 laps with bolts through them are plenty sturdy on my bench: 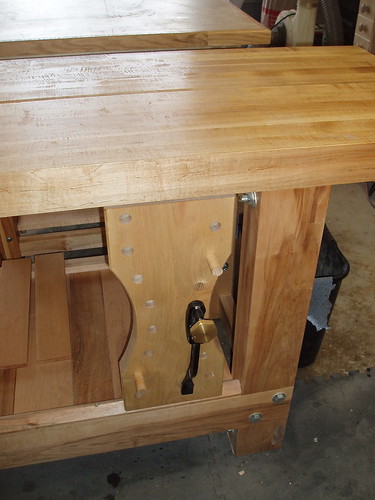
|
|
|
Post by RiverWalker on May 4, 2010 11:16:57 GMT -6
Tim, thats actually quite reassuring, I was half concerned that might go to the point of getting it all done, then going to using it, and the whole thing tip over or something from just not being big enough. Why can't you remove the carpet,if you leave it you are going to have to remove it in the near future anyway,,,,,,,,,,,,,wear patterns,spills,abrasives working on carpet fibers etc dick lol, its a to be honest, relatively crappy apartment, so removing the carpet really isn't an option. wear patterns I'm not concerned with, not expecting to spill much of anything, or anything like that, that after removal of the tools and stuff would not seem like normal degrees of wear. (they care enough that they'd likely be unhappy with the carpet not being there, but not by it being heavily worn, I don't think) at the moment my planning is heavily based off of the "Kirby" Bench, but adding the sled feet from the "Fortune/Nelson" bench. I am not sure I am particularly impressed with the end-oriented nut and bolt (the nut in a drilled/routed hole type thing pulling the joint closed), it seems like that would be awkward and/or mistake prone, and thus I think I'm going more in the direction of through tenons. my current musing is wedging the leg-foot connections, the tapered pin mechanism it describes for the side stretchers, and through-bolts for the left-right stretchers. though if it would be much stronger to make the entire base structure unable to be taken apart, it might be worth the hassle of having to move the whole base in one piece, and since its not going to be that ginormous, it would not be THAT terrible to move. the method it has on the kirby bench, looks interesting, with doubling(ish) the mortise length of the stretcher-leg joint by attaching a short piece to the stretcher near the joint. has anyone had experience using that theory? I would think that the racking force might sheer the glue joint between the two pieces, but maybe its not really a problem? or could be solved by doweling it as well as glue? Jerry, at the moment I think the option I'm stuck with for the vice, is a crappy knock off "record" style face vice. while I'd like to be able to go with a leg vice like that(the throat or whatever on those, looks like it'd be really nice for some of the smaller scale dovetailing and stuff I expect to be doing) but I am not sure I can swing the difference in cost at the moment. but, I may change my design plans a little to make it take less renovating to fit it with a leg vice later on.... gonna have to look at it more. but hey thats what plans on paper are for. Kevin, since what I'm looking at is probably about 2' deep and 4' long, and from the sound of it, and a bit over 3' high, I am not sure that for me it'll be worth being able to take it apart without damaging it, so I may use wedges and such. drawboring is the thing with pins, where the holes in the mortise and in the tenon are misaligned very slightly, so that when the pin is driven in it pulls the joint super-tight, right? you guys seriously rock. I'm going to make sure to post the plans I come up with once I get them a bit more worked out, and see what you all think. speaking of which though, anyone know a free CAD program that might be able to be downloaded, that could be used for making up such plans all professional like?
|
|
sawduster
Moderator
The Motley Crew
Posts: 1,831
|
Post by sawduster on May 4, 2010 11:50:19 GMT -6
Not a true CAD program, but I use the free version of Google SketchUp, available here. The Pro version cost several hundred dollars, but the free version does most of the same stuff. I had tried several different CAD packages and just couldn't get the hang. I was using SketchUp within a short time of beginning using it. Several folks here use it and there are forums on line with lots of folks who are real helpful. Other than the depth available above the screw with the leg vise, my biggest reason for choosing it was that it was relatively cheap as far as vises go. Other than the wooden parts, the only thing to buy is the screw which is available from Lee Valley.
|
|
|
Post by TDHofstetter on May 4, 2010 12:08:49 GMT -6
I'll second SketchUp! I LOVE that thing! For years I searched for a decently comfortable CAD app that worked the way my mind does, and when they brought this thing out I fell for it like a barrel of monkeys. Or something like that.  Really - I do anything from timberframe drawings to to-the-thousandth machining drawings with it... it's fast, it's mostly intuitive, it does 3D drawings nearly naturally. Six clicks draws you a 3D rectangle - like a board, for example. I just drew up a birdhouse plan for Marie - she's got a friend who's hauling a whole passel of 4H kids here to build birdhouses - that uses common dimensional lumber and actually WORKS without filling with rain, gumming up, and growing sunflowers. Fifteen minutes to draw it including thinking time, fully 3D, removable top. She couldn't find an acceptable plan on the Internet... 
|
|
sawduster
Moderator
The Motley Crew
Posts: 1,831
|
Post by sawduster on May 4, 2010 12:46:13 GMT -6
And a plethora of free and cheap add-in tools including a number wood working specific ones.
|
|
|
Post by imahic on May 4, 2010 13:13:36 GMT -6
I'm not very profficient with Sketch up like Jerry and some of the others are. But what I have done with it seems pretty cool and easy to use. My wife and I both got degrees in computer aided drawing and learned AutoCad. I enjoyed using it when I had a copy of it but it has been several years since I have used it.
As noted by all the other guys, heigth of your workbench is pretty much a personal preference based on what is most comfortable to you. I am also 6'2 and all of mine are 36" high with one exception. I have one bench that is about 40 " high but I am usually sitting on a stool when I am doing anything at it.
|
|
Joe Lyddon
WoW Member
Banned.
Sam Maloof & I Dec. 2, 2005
Posts: 2,507
|
Post by Joe Lyddon on May 4, 2010 13:35:25 GMT -6
The Woodsmith Shop TV show, this morning on the Create PBS channel, featured a workbench that could be built in a weekend... from Douglas Fir 2x6's, MDF, hardwood, carriage bolts, glue & screws... Installed a vise too... Was a nice, COOL, Simple, bench... 
|
|
|
Post by Safetyboy on May 4, 2010 13:48:16 GMT -6
Jerry, at the moment I think the option I'm stuck with for the vice, is a crappy knock off "record" style face vice. while I'd like to be able to go with a leg vice like that(the throat or whatever on those, looks like it'd be really nice for some of the smaller scale dovetailing and stuff I expect to be doing) but I am not sure I can swing the difference in cost at the moment. Leg vise is just about the cheapest vice you can get, actually - I think the screw from LV somebody else mentioned is only about $35. Kevin, since what I'm looking at is probably about 2' deep and 4' long, and from the sound of it, and a bit over 3' high, I am not sure that for me it'll be worth being able to take it apart without damaging it, so I may use wedges and such. drawboring is the thing with pins, where the holes in the mortise and in the tenon are misaligned very slightly, so that when the pin is driven in it pulls the joint super-tight, right? Yeah, that's it. Useful if your stretcher is longer than your available clamps.
|
|
|
Post by RiverWalker on May 4, 2010 21:38:00 GMT -6
Jerry, at the moment I think the option I'm stuck with for the vice, is a crappy knock off "record" style face vice. while I'd like to be able to go with a leg vice like that(the throat or whatever on those, looks like it'd be really nice for some of the smaller scale dovetailing and stuff I expect to be doing) but I am not sure I can swing the difference in cost at the moment. Leg vise is just about the cheapest vice you can get, actually - I think the screw from LV somebody else mentioned is only about $35. well the idea I had originally figured was a crappy, small little vice that would be more like $20 bucks, and minimally functional as a vice. but yeah, doing a leg vice with that screw would be substantially better, and the more I think about it the more I think I would be happier with that, so I'll be adjusting things and all to see about going at it that way. still depends on our tax return being what we expect, and coming through....but not really worried about that. now to try to finish, and translate the plans I have into that SketchUP program so I can share my plans and adjust them with advice from here.
|
|
|
Post by RiverWalker on May 7, 2010 0:30:52 GMT -6
well, I've got most of a workbench design put together in SketchUp... not sure what the best way to share the actual file so others can look at what I have. 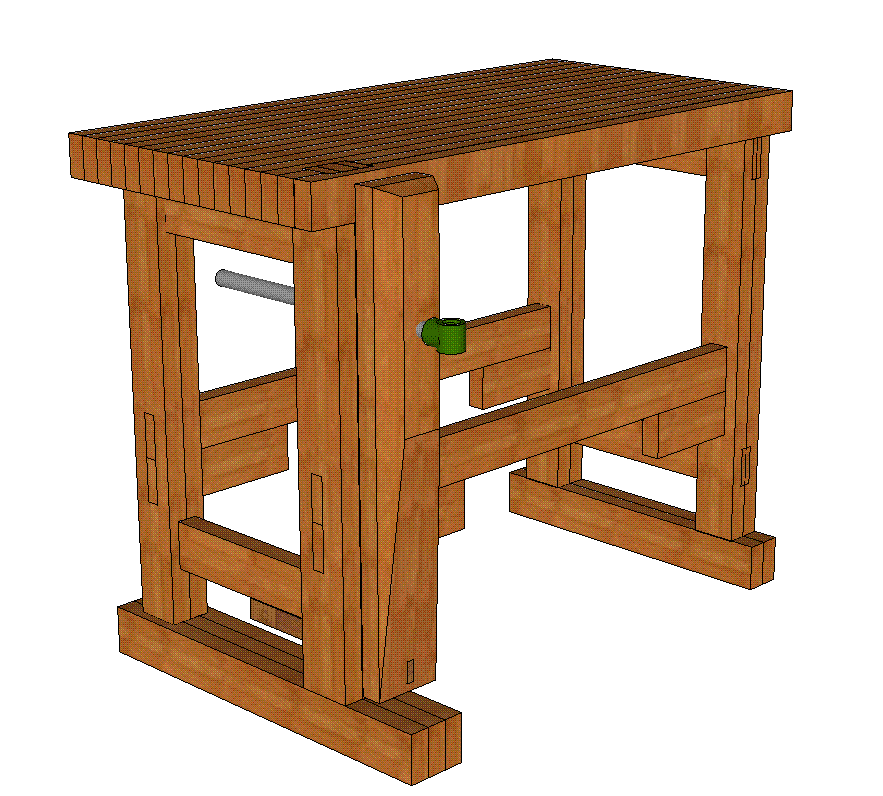 heres a screenshot of what I have so far.... I don't have all the virtual mortices "cut" yet, nor depictions (or descisions, really...) of how I want to fasten it all. I am figuring the top, the leg-vice-leg, and leg-vice wood to be the same SYP. the rest to be 2x4's, I think the guy said something about it being douglas fir? not sure if that is a problem, good or bad thing. not like its nailed down anyway. the bevels on the vice portion are not decisive, more suggestive of the idea I have in mind. I realize theres probably not much to be seen from this one shot, just giving a bit of progress for anyone who might be at all curious or interested. oh, and wondering if anyone has a good way to share the actual SketchUp file so people might be able to give a better opinion on the design? edit: oh, and gross measurements to give a better idea.. the top is 2' deep, 4' wide, the vice screw is about 8" below the top, the sled foot on the vice side projects about 6" past the front edge of the bench, the vice-leg laminations are 4" deep, and 3 wide(so 4"x4.5") from the top to the bottom of the foot is about 38". most of the mortices have a 1/4" shoulder. pretty much the rest of the construction is 2x4's, (using 1.5x3.5 as actual measurement)
|
|
sawduster
Moderator
The Motley Crew
Posts: 1,831
|
Post by sawduster on May 7, 2010 7:33:48 GMT -6
Unless you've got some web space to store the file on, not many options other than emailing them to folks who request it. There is also the 3DWarehouse that you can upload to, but then it becomes available to the whole world. It is also huge so searching for a particular item can be testy, but you could paste a link to it into a thread here. Doug fir would be good choice for the top as well as the legs and chassis. If the Doug Fir is cheaper in your neck of the woods, go with that. Only thing you might consider is to use some hard 8/4 hardwood for the vise, maybe maple, but any hard wood would work. Mine is white oak because that is plentiful and relatively cheap around these parts.
|
|
|
Post by RiverWalker on May 7, 2010 12:16:28 GMT -6
Unless you've got some web space to store the file on, not many options other than emailing them to folks who request it. There is also the 3DWarehouse that you can upload to, but then it becomes available to the whole world. It is also huge so searching for a particular item can be testy, but you could paste a link to it into a thread here. Doug fir would be good choice for the top as well as the legs and chassis. If the Doug Fir is cheaper in your neck of the woods, go with that. Only thing you might consider is to use some hard 8/4 hardwood for the vise, maybe maple, but any hard wood would work. Mine is white oak because that is plentiful and relatively cheap around these parts. ooh, figured out the 3D Warehouse thing. heres the link for it. sketchup.google.com/3dwarehouse/details?mid=bc7303d024b13e2a6c78c987f7f5b618as far as the material goes, I'm not sure it'd be cheaper or not, I'll have to look into that. the way I'm figuring it is that a most of a 2"x12"x10' would cover the laminations for the vice leg, and the vice itself, which seems relatively tidy. I was thinking about something like using a strip of maple set into the structural wood to spread out the load more and take some of the wear. I was figuring this might be the most beneficial where the nut attaches on the back side of the leg,to spread the force across the laminations more evenly. would something like that, either using another piece of the same wood, or a harder wood, be beneficial? just on the back, or where the front of the screw attaches as well? I imagine it would look kinda cool asthetically, but would it be functionally worthwhile? I was thinking of doing something similar "grommeting" where the bar at the bottom of the vice goes through the leg. oh and the vice leg post goes through the top, I am figuring that to just try to be fitted tight, but not actually fastened through the top. that way for transport(weight, more than bulk, consideration) the top could be lifted off. I am thinking that it'd be neat to be able to make it so the only metal in the whole thing was the vice screw hardware. its probably a little ambitious, but I think I'm up to it. :-)
|
|
tw
WoW Member
Posts: 126
|
Post by tw on May 9, 2010 4:25:00 GMT -6
Welcome aboard. A did almost start feeling alone being a young hand tool woodworker  In my oppinion 4 foot long is a bit short. I outgrew a bench like that in just three years. Planing a board by hand is much easier if the bench is longer than the board. My present bench is about 6'4"long and has a proper tailscrew vice. Otherwise your design makes good sence to me.
|
|
|
Post by RiverWalker on May 9, 2010 11:19:06 GMT -6
4' is definitely not that big, but I think for where I am at right now, it should be fine. extremely time cramped, very cost-cramped, and honestly I can't think of any projects that would include parts over 4' long, that I'm likely to have much of any interest in doing any time soon. I am sure eventually I might, but I'm figuring by then I'll probably want to do a new bench, or an extension, or something like that anyway. I am aware of the issue you mention though, and have considered that, :-) now I have a particular point I'm hung up on that I'd like opinions on the joint between the upper stretcher on the left side, and the vice-leg. heres the three options I've worked out/considered, and I'm not sure what the best one would be. figuring actual measurements of 1.5 x 3.5(2x4) for the stretcher, and 1.5x4(2x10 ripped to 4") laminated 3 wide for the leg. 1: 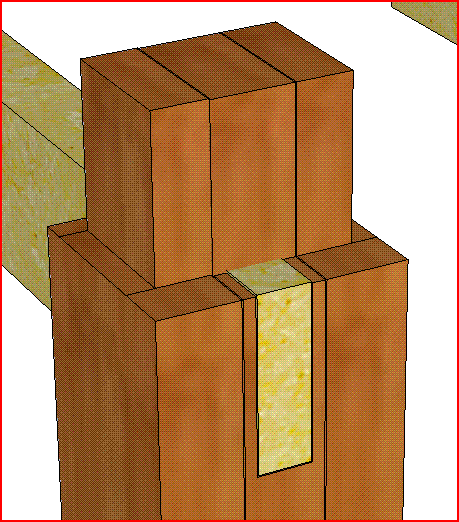 2: 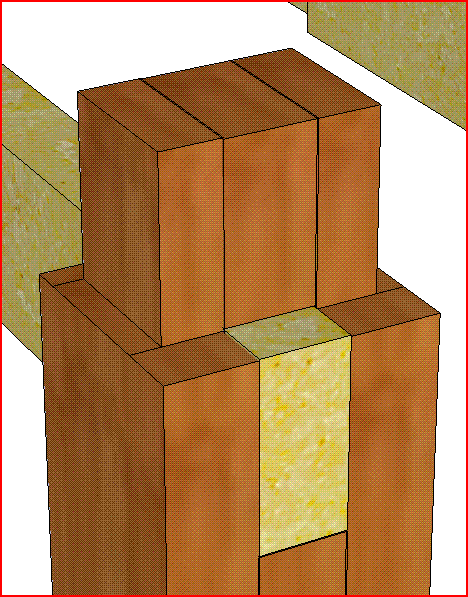 3: 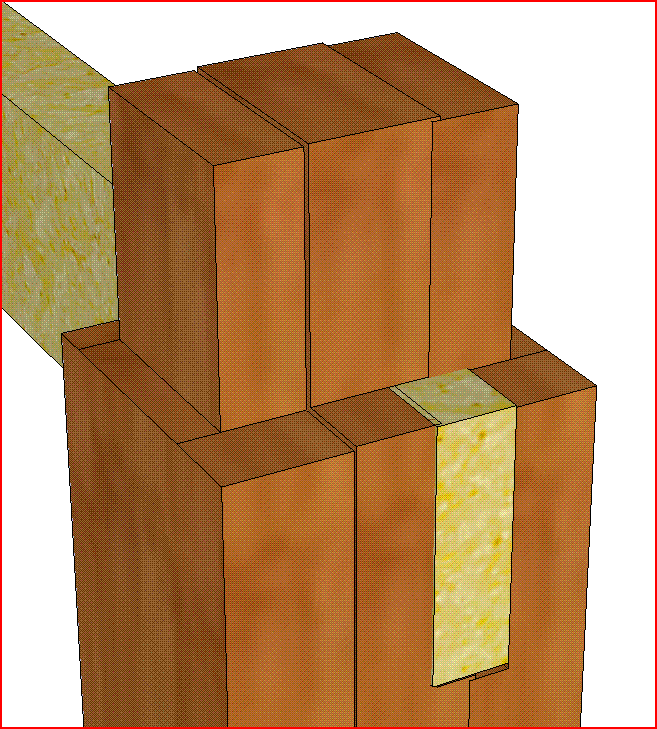 in the first and third options, the tenon having a 1/4" shoulder on 3 sides(not the top-side) in the second option, it being just a 1/4" shoulder on the bottom-side, the rest being straight through. in case the pictures aren't perfectly clear, the first option has the mortice being through the center beam of the lamination, leaving a 1/4"... webbing(?) on each side. the second is simply having the stretcher at its almost full dimension, going through between the first and third beams of the leg. the third, the mortice straddles the second and third beams of the lamination (in essence, being more like the mortice of the other 3 legs, with a third beam tacked on the outside-side) if it wasn't clear from the other image/file, the vice-leg is planned to go entirely through the top, with a 1 inch shoulder on the face-side, half inch shoulder on the back side, and 1/4" shoulders on the left and right. I had originally figured on option 3, but modeling it up, it looked REALLY whonky, and I was concerned about there being potentially some weird twisting geometry/mechanics with the vice or something from having the stretcher off-center. but I am not sure if any benefit from having a mortice through the center beam, rather than just having a gap between the middle of the beam and the part that goes through the bench top, would be worthwhile.
|
|
|
Post by dcarter636 on May 9, 2010 13:04:02 GMT -6
I'm not into sketch-up so I'll try with verbiage.
I would reduce the top stretcher tenon to 1"x2" so that it doesn't break through the shoulder of the benchtop registration tenon on the top end of the vise leg. Center it on the leg to keep the loading symmetrical and because it's simpler to lay out.
I would also reduce the benchtop registration tenon to 1 1/2"x3" (that's almost a 2x4), which is plenty strong without compromising so much of the of the benchtop edge strength.
Also once you have properly laminated those boards with Tite Bond II, III, or the equivalent think of them as homogeneous wood, don't worry about where the glue joints were when laying out your joint features.
Big tenons and overly strong joints are fine things, but keep in mind that the forces that would challenge M&T joints half the size that you show here will tip this 2'x4' bench up on end.
|
|